Troubleshooting Guide for Bottle Conveyor Machine: Keeping Production on Track
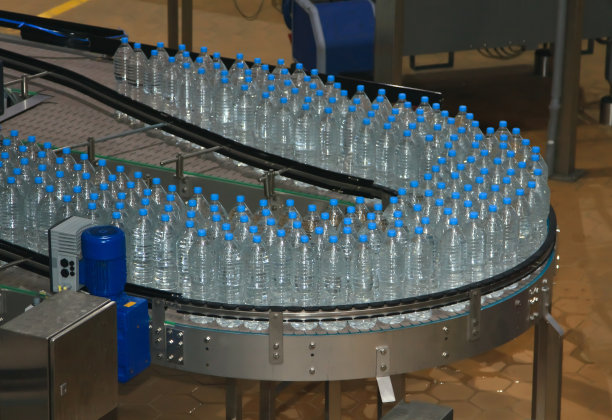
Plastic water bottles on conveyor and water bottling machine industry
The bottle conveyor machine is a commonly used equipment on production lines, designed to transport bottles from one location to another. It features a modular structure with interchangeable parts, compact design, low noise, easy installation, and maintenance. It can be customized for different types of bottles, with glass bottles typically using stainless steel conveyors and PET bottles using plastic conveyors.
However, despite being a reliable device, occasional malfunctions can occur with the bottle conveyor machine. These malfunctions can disrupt the production line and negatively impact efficiency. Therefore, it is crucial to understand and be able to troubleshoot issues with the bottle conveyor machine promptly.
Here are some common bottle conveyor machine malfunctions and their troubleshooting methods:
- Conveyor belt stops moving: If the conveyor belt stops moving, first check the power supply. Ensure that the power plug on the conveyor belt is securely connected, and the power switch is turned on. If the power supply is fine, it may be a motor issue. Inspect the motor for blockages or damage and replace it if necessary.
- Slow or uneven movement of the conveyor belt: If the conveyor belt moves slowly or unevenly during operation, it could be due to improper tensioning of the belt or damaged bearings. Check the tensioning device of the conveyor belt and ensure it is properly adjusted. Additionally, inspect the bearings for lubrication or replacement needs.
- Bottle blockage or tipping: If bottles get blocked or tipped during the conveying process, it could be due to the conveyor belt's tilt or incorrect spacing between bottles. Check the installation of the conveyor belt for levelness and adjust the spacing between bottles.
- Abnormal noise: If the conveyor belt generates abnormal noise, it may be caused by loose drive chains or friction between the belt and the guide rails. Check the tension of the chains and lubricate them, as well as the guide rails, to reduce friction.
- Control system malfunction: If the control system malfunctions, the conveyor belt may not operate correctly. Check the power connection of the control system and inspect electronic components for damage. Repair or replace electronic components of the control system if necessary.
Before performing any maintenance or troubleshooting procedures, ensure to disconnect the power and follow safety protocols. If you are unsure about how to troubleshoot or perform repairs, seek assistance from professional technicians.
HZM Machinery is a professional supplier of bottle conveyor machines, offering comprehensive after-sales service. Whether it's equipment installation or troubleshooting, they have an experienced technical team to provide support and assistance. If you encounter any malfunction issues while using the bottle conveyor machine, feel free to contact their after-sales service, as they are dedicated to providing solutions.
In conclusion, the bottle conveyor machine is a common equipment found on production lines. While occasional malfunctions may occur, by understanding common issues and their troubleshooting methods and collaborating with a professional supplier, we can promptly address malfunctions and ensure the smooth operation of the production line.
TAG: Bottle Conveyor conveyor machine



-
Beverage Filling Line – Juice, Water, Soft Drinks, cola, Beer
-
Automatic Pure Water Bottling Filling Machine
-
Fully Automatic Beverage Filling Machine
-
3-In-1 Water Bottle Filling Machine
-
Conveyor Belt System For PET Bottle And GLASS Bottle
-
Bottle Water & Beverage Conveyor System
-
Bottle Conveyor
-
Packs Conveyor
-
Bottle Air Conveyor
-
Beverage Filling Line – Juice, Water, Soft Drinks, cola, BeerJul , 21 /2025
-
Automatic Pure Water Bottling Filling MachineDec , 21 /2023
-
Fully Automatic Beverage Filling MachineOct , 11 /2023
-
3-In-1 Water Bottle Filling MachineOct , 10 /2023
-
Why Your Bottling Line Needs A Total Conveyor SolutionApr , 27 /2023
-
10 Tips for Procuring High-Quality Conveyor Machines: Ensuring Smooth Production Line OperationsJun , 25 /2023
-
The Diverse Applications of Bottle Conveyors in Various IndustriesJun , 25 /2023
-
HZM Machinery: A Trusted Bottle Conveyor Manufacturer Offering Factory Direct PricesJun , 25 /2023
-
Your Reliable Conveyor Machine ManufacturerJul , 06 /2023
-
Air conveyor systemsJul , 12 /2023